In modern automotive technology, Printed Circuit Boards (PCBs) play a pivotal role, serving as the nerve center of electronic systems. The demand for smarter, more reliable vehicles has thrust the realm of PCB design into the spotlight.
This blog post delves into the nuances of advanced PCB design for automotive applications, unraveling the complexities and providing valuable insights for engineers navigating this challenging terrain.
Overview of Automotive Electronics and PCBs
In the automotive realm, PCBs form the backbone of electronic systems, facilitating seamless communication between various components. As the automotive landscape evolves, PCBs must align with stringent requirements, balancing durability, reliability, and compactness to meet the demands of the road.
The journey of PCBs in automotive systems traces back to their foundational role in basic electrical connections within early vehicles. Over time, their role has expanded dramatically to keep pace with technological advancements. Today’s automotive PCBs are not merely conduits; they are sophisticated platforms that enable innovation in vehicle design, safety, and performance.
- Durability Amidst Harsh Conditions: The automotive environment is unforgiving, subjecting PCBs to a myriad of challenges. From extreme temperatures to mechanical vibrations, these circuit boards must withstand harsh conditions without compromising functionality. Robust designs are essential to ensure longevity and consistent performance.
- Reliability as a Non-Negotiable Factor: Reliability is paramount in automotive electronics. The reliability of PCBs directly influences the overall performance and safety of vehicles. Whether navigating city traffic or cruising at high speeds, PCBs must operate flawlessly to instill confidence in the reliability of electronic systems.
- Compact Design in a Shrinking Space: As automotive design trends towards sleeker, aerodynamic profiles, the space available for electronic components, including PCBs, continues to diminish. Compactness is not just a design preference but a necessity. PCBs must embrace miniaturization without compromising their core functionalities.
Compliance with Industry Standards and Regulations
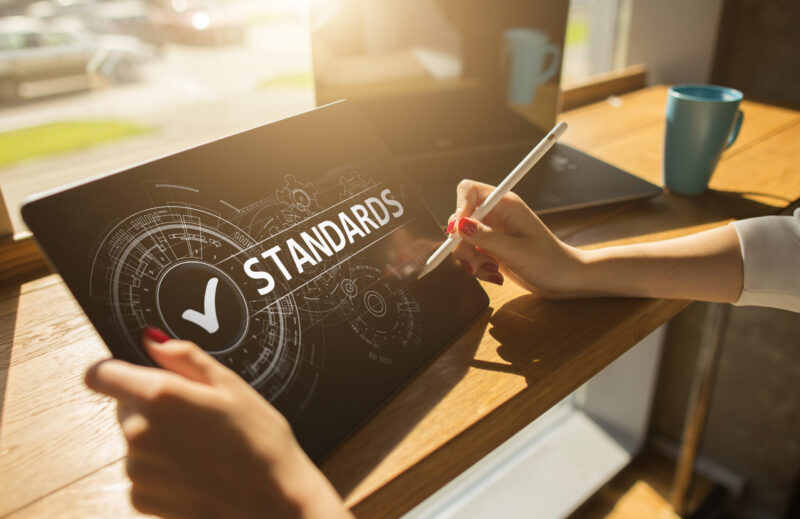
According to the experts from Vinatronic, straying from the beaten path is not an option in the automotive industry. Compliance with rigorous standards and regulations is paramount. Automotive PCB designers must navigate a labyrinth of guidelines to ensure their creations adhere to the highest quality and safety benchmarks.
High-Speed Signal Integrity
The automotive ecosystem demands a meticulous approach to signal integrity. Any compromise can lead to communication breakdowns between crucial components. Techniques such as impedance control and careful routing are essential to minimize signal degradation and reflections.
Power Distribution and Management
Power is the lifeblood of automotive electronics. Efficient distribution and management are imperative. Designers must strategize to minimize power losses, ensuring optimal performance while navigating the constraints of compact spaces within vehicles.
Thermal Management
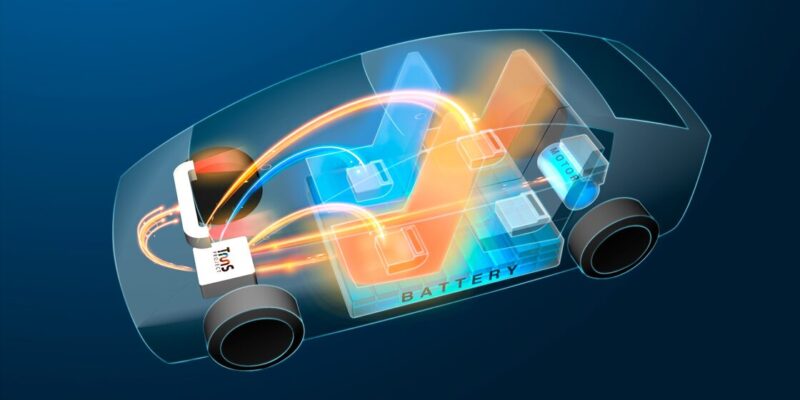
The harsh environment within a vehicle necessitates vigilant thermal management. Heat dissipation becomes a critical consideration to prevent component failure. Designers employ innovative thermal design techniques, leveraging heat sinks and advanced materials to maintain PCB reliability.
Effective thermal management is not a luxury but a necessity to ensure the longevity and consistent performance of automotive electronics.
Designers tasked with navigating this thermal minefield employ a repertoire of innovative techniques to address heat dissipation. At the forefront of these strategies is the use of advanced materials that possess superior thermal conductivity. These materials efficiently draw heat away from sensitive components, preventing overheating and potential failure.
- Heat Sinks: A cornerstone of thermal management, heat sinks are meticulously integrated into PCB designs. These passive heat exchangers enhance surface area and dissipate heat through conduction and convection. Strategic placement of heat sinks, coupled with the judicious selection of materials, significantly contributes to mitigating temperature-induced stresses.
- Conductive Cooling: In the pursuit of thermal equilibrium, conductive cooling techniques play a pivotal role. This involves optimizing the layout of components on the PCB to enhance the natural conduction of heat away from critical areas. By strategically arranging components and ensuring efficient thermal pathways, designers effectively minimize temperature differentials across the board.
- Fluid Cooling Systems: In certain applications, particularly those demanding heightened thermal control, fluid cooling systems come into play. Incorporating channels or tubes filled with coolants adjacent to heat-generating components facilitates efficient heat dissipation. This sophisticated approach ensures precise temperature regulation even in the most demanding environments.
The selection of materials in PCB construction is a critical determinant of thermal resilience. Thermally conductive substrates, such as metal core PCBs, enhance heat dissipation. Moreover, the integration of thermally conductive fillers in the base material further augments the board’s ability to manage temperature fluctuations.
EMI/EMC Considerations
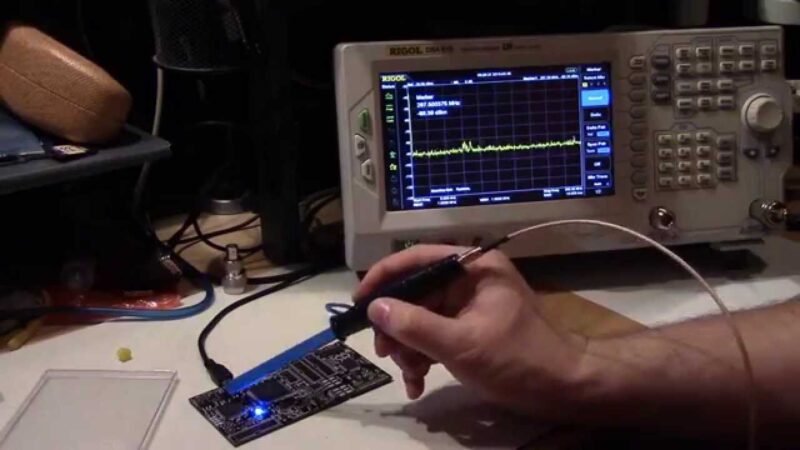
The automotive landscape is rife with electromagnetic challenges. Achieving electromagnetic compatibility (EMC) is not just a checkbox; it’s a meticulous process. Designers must employ shielding techniques and proper grounding to minimize electromagnetic interference and ensure compliance with standards.
Selection of Automotive-Grade Components
Not all components are created equal, especially in the unforgiving environment of a car. Automotive-grade components designed to withstand temperature fluctuations, vibrations, and other environmental stressors are the unsung heroes of PCB design for automotive applications.
Optimal Component Placement
The arrangement of components on a PCB is akin to choreographing a dance. Strategic placement minimizes signal crosstalk and interference, ensuring the harmonious performance of the entire electronic ensemble within the confines of the vehicle.
Rigorous Testing Procedures
Functional tests form the initial frontier, delving into the operational prowess of the PCB. These assessments go beyond ensuring that components switch on and off as intended. They meticulously scrutinize the functionality of intricate circuits, evaluating how well the PCB translates design intent into real-world functionality. Functional tests not only affirm the operational capability but also serve as the first line of defense against latent design flaws.
Environmental stress tests represent a pivotal phase in the testing hierarchy. These assessments subject PCBs to a spectrum of conditions that mimic the diverse challenges of the actual vehicular environment. From temperature extremes to mechanical vibrations, environmental stress tests simulate the rigors of the road. By replicating real-world scenarios, designers gain insights into how the PCB will respond under adverse conditions, ensuring its resilience against the harshest elements.
Reliability and Endurance Testing
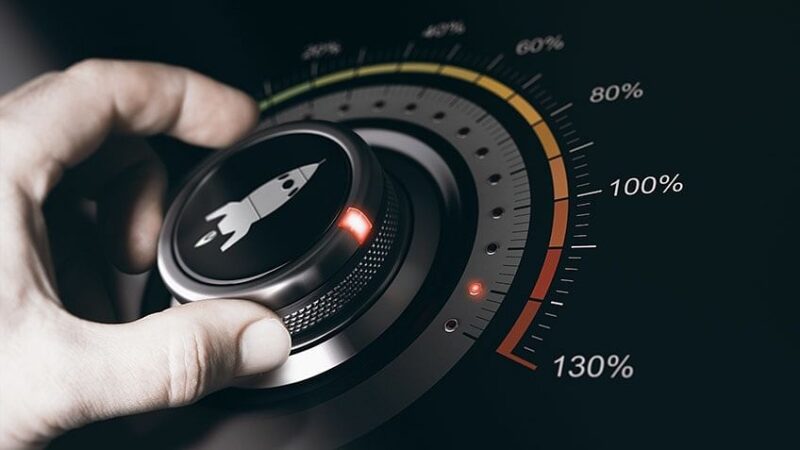
The road is unpredictable, and so must the PCBs that navigate it. Endurance testing under extreme conditions, mimicking the harshest environments, is a necessity. Only by subjecting PCBs to the rigors of real-world conditions can their true reliability be ascertained.
Conclusion
In the ever-evolving landscape of automotive electronics, advanced PCB design stands as a linchpin, holding together the intricate web of technology that defines modern vehicles. As we journey forward, the emphasis on durability, reliability, and compactness will only intensify.